Toilet paper rarely makes headlines. But perhaps no other commercial product save hand sanitizer has become as emblematic of the global anxieties caused by the coronavirus pandemic as toilet paper – or the lack thereof.
Unlike hand sanitizer, however, most experts agree that the rush to hoard toilet paper stems from an illogical anxiety, one planted in the notion that the supply chain will suddenly break: that manufacturers will abruptly stop producing toilet paper and that supermarkets will be unable to stock their shelves.
5 stages of the operations and supply chain management crisis lifecycle
From the early days of the outbreak, COVID-19 exposed vulnerabilities in global supply chains and operations management. Here, professor Jaume Ribera breaks down the life cycle of operations management and supply-chain crises into five stages, and gives recommendations on how companies can make themselves less vulnerable to shocks.
1. Prevention
Ribera says that if companies haven’t already done their supply-chain homework, they should start doing it now. Subsequent actions will build on this first step.
- Map your existing supply chain (including your customers and your supplier’s supplier, and where they’re located, their current capacity and their inventory).
- Understand real demand as distinct from distortions from panic buying.
- Anticipate where disruptions are most likely to occur.
- Look for alternatives.
- Carry out supply-chain stress tests. Governments around the world have learned the importance of this the hard way.
2. Detection
Next, monitor your supply chain based on what you discovered from your mapping exercise.
- Distinguish between signals and noise: Pay attention to the bullwhip effect, where unstable buyer behavior causes wild fluctuations further up the chain.
- Use knowledge frameworks such as this known-unknown matrix:
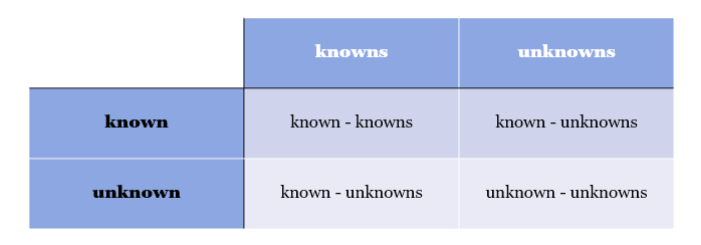
3. Survival
At this stage, you need to do anything that you haven’t done yet.
- Identify emerging action plans regarding your people and resources.
- Make the best use of scarce resources.
- Review your governance practices: Weigh the pros and cons of keeping centralized command and control versus making information transparent to other people.
4. Recovery
Here’s where you adjust your operations to the new normal: For example, based on your newfound experience of online or remote working, you may find this way of working becomes more widespread in your organization.
- Decide on a concrete recovery plan. It won’t just be picking up where you left off.
- Revise the previous stages in light of your findings.
- Question previous decisions. Do you make or do you buy in what you need? Does more local sourcing and more local capacity make better sense for your current situation?
5. Compete again
They say a crisis is an opportunity, and in this case, the opportunity would be to innovate your operations and supply chains.
- Build learnings into future impact planning: This is especially important if a another wave of coronavirus infections should occur.
- Decide how you will compete in the new normal.
While it may be too late for some companies, Ribera urges everyone to use their time wisely to review these five steps. However long this crisis lasts, it’s important to be ready for the new reality.
Want to learn more? Watch this open-access online session with Prof. Ribera, where he discusses operations management and supply chains during turbulent times. Or immerse yourself in IESE’s executive programs that ensure managers acquire all the skills and knowledge they need to detect supply chain vulnerabilities and manage operations effectively in the postcovid era.